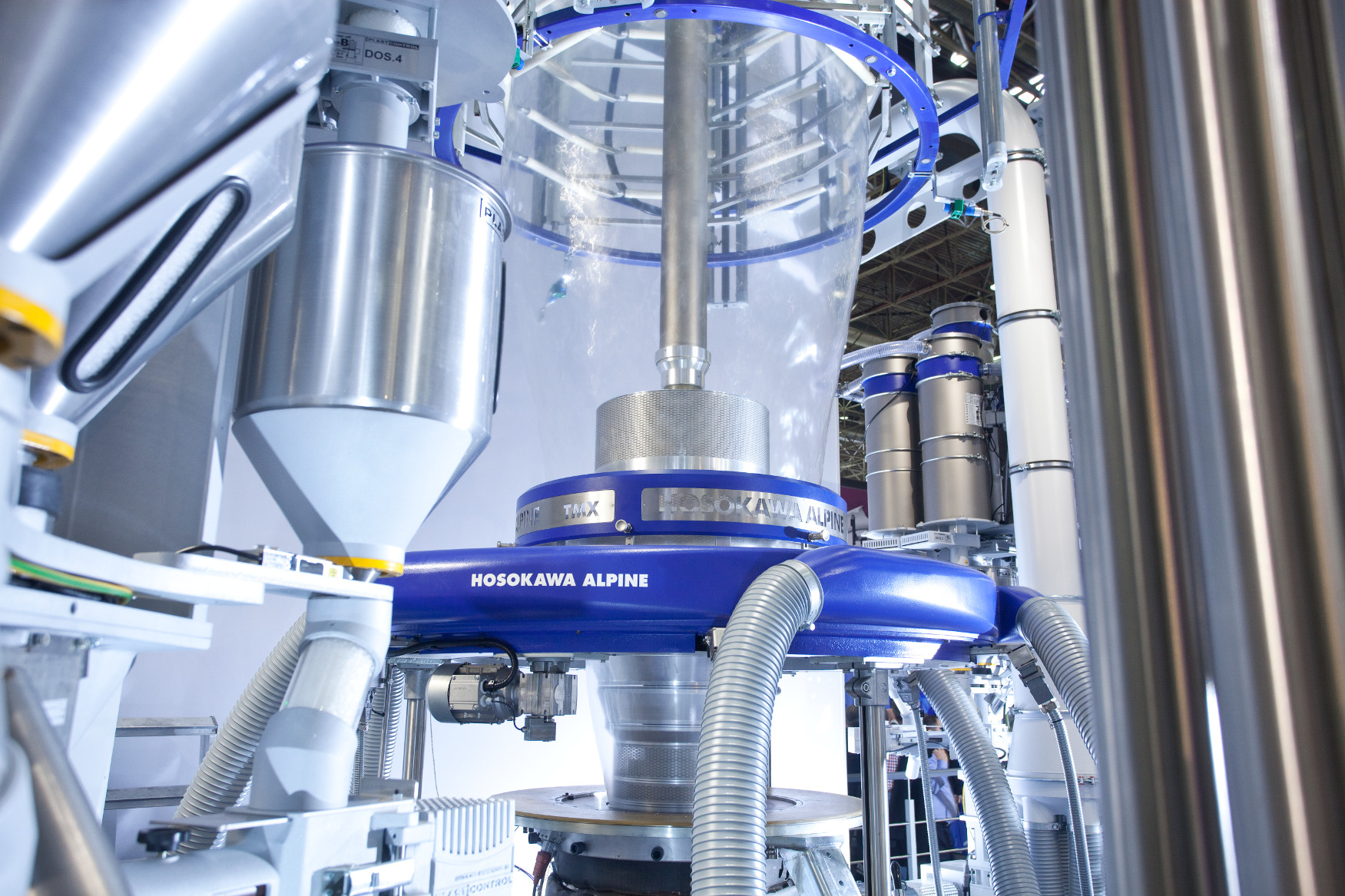
A Blown Film Machine is a specialized industrial apparatus used predominantly in the manufacturing of plastic films, which are critical for packaging industries, agricultural films, and various other applications. The machine operates by melting plastic polymers and extruding them through a die. As the plastic exits the die, air is blown into the film to form a tubular bubble. This process leads to the creation of thin, continuous sheets of plastic film with precise dimensional properties.
1. The Blown Film Extrusion Process
Blown film extrusion involves feeding raw plastic material, often polyethylene, into an extruder, where it is heated and transformed Blown Film Machine a molten state. The molten plastic is forced through a circular die, emerging as a thin-walled tube. Air is introduced into the center of the tube, expanding it to the desired diameter. This method is known for producing strong films with excellent uniformity in thickness.
2. Components of a Blown Film Machine
A typical blown film machine consists of several core components:
- Extruder: Where the plastic material is melted and pressurized.
- Die Head: Shapes the molten plastic into a tubular form.
- Air Ring: Cools and stabilizes the bubble as it forms.
- Winder: Collects the cooled film, typically in rolls for further processing.
3. Types of Polymers Used
Blown film machines are versatile and can process a variety of plastic polymers. The most common types include:
- Low-Density Polyethylene (LDPE): Known for its flexibility and transparency, LDPE is widely used in bags and wrapping films.
- High-Density Polyethylene (HDPE): Offers higher strength and stiffness, making it suitable for applications like grocery bags.
- Polypropylene (PP): Known for higher temperature resistance, PP films are used in food packaging and medical applications.
4. Advantages of Blown Film Technology
One of the key benefits of the blown film process is its ability to create films with consistent thickness across large areas. The method is highly efficient and produces minimal waste. Additionally, the process can be fine-tuned to create films with specific characteristics like strength, clarity, and barrier properties, depending on the intended use.
5. Applications of Blown Film Products
Blown film products are ubiquitous in everyday life. They are essential in industries such as:
- Food Packaging: Transparent and flexible films are commonly used for food wrap, bags, and pouches.
- Agriculture: Blown films are used for greenhouse covers, silage wraps, and mulch films.
- Industrial Packaging: Heavy-duty films are used for pallet covers, shrink wraps, and other protective packaging materials.
6. Innovations in Blown Film Technology
Recent advancements in blown film technology have focused on increasing production efficiency, improving film quality, and minimizing environmental impact. Co-extrusion technology, for example, allows for the production of multilayer films with different properties on each layer, enhancing the film’s performance in packaging applications. Additionally, modern machines are increasingly equipped with automated control systems, which improve precision and reduce the need for manual adjustments.
7. Environmental Considerations
As concerns about plastic waste grow, the industry is looking for ways to make blown film production more sustainable. Many manufacturers are experimenting with bio-based polymers and biodegradable materials. Additionally, efforts are being made to increase the recyclability of plastic films produced by blown film machines. Recycling-friendly designs and the incorporation of recycled content into the films are also trends gaining traction.
8. Challenges and Considerations in Operation
Operating a blown film machine requires expertise, as factors like air flow, cooling, and polymer temperature must be carefully controlled to produce high-quality films. Variations in any of these parameters can lead to defects such as film sagging or uneven thickness. Regular maintenance is also essential to ensure that the machine operates efficiently over time.
9. Future Prospects of Blown Film Machines
The demand for blown film machines is expected to rise as global packaging needs increase, particularly in emerging markets. The push towards sustainability will likely drive further innovation, with a focus on machines that can handle a wider range of eco-friendly materials without compromising on production efficiency.
10. Conclusion
In summary, the Blown Film Machine is a critical piece of equipment in the plastic film manufacturing industry. Its ability to produce versatile, strong, and cost-effective films makes it invaluable for packaging, agricultural, and industrial applications. As technology evolves, the potential for more sustainable and efficient film production continues to grow, offering exciting prospects for the future of the industry.